Get Durable and Accurate Custom Brass CNC Machined Parts
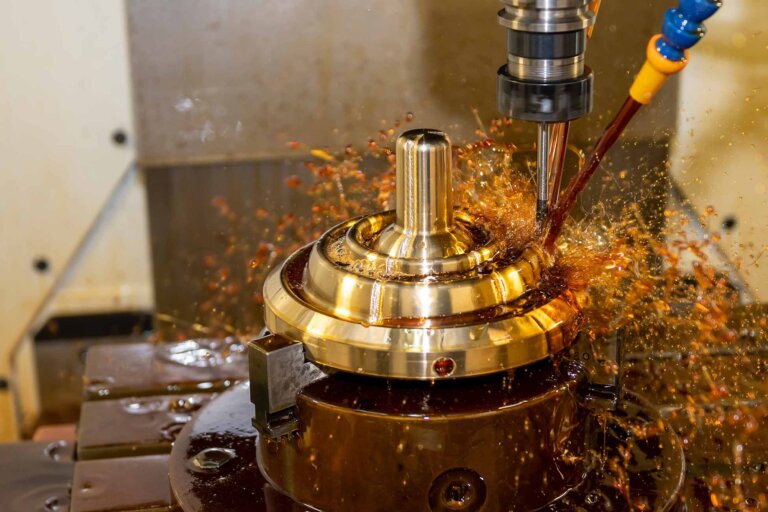
In today’s competitive manufacturing landscape, precision, reliability, nd material performance are non-negotiable. Brass—an alloy of copper and zinc—has long been prized for its excellent machinability, corrosion resistance, electrical conductivity, and attractive finish. When combined with CNC (Computer Numerical Control) machining, brass becomes an optimal solution for high-precision, durable components across a multitude of industries. This article explores why you should get durable and accurate custom brass cnc parts, the key advantages they offer, common processes, and best practices for selecting a machining partner.
Why Choose Brass for CNC Machining?
- Superior Machinability
Brass ranks among the easiest metals to machine. Grades such as C36000 (free-machining brass) contain lead additions that break chips and reduce tool wear, allowing for tight tolerances (often ±0.01 mm) and complex geometries without compromising cycle times. - Corrosion Resistance
Unlike steel or iron, brass resists rust and tarnish naturally. This makes it ideal for plumbing fittings, marine hardware, and outdoor applications where moisture or salt exposure is a concern. - Electrical and Thermal Conductivity
Brass’s excellent conductivity supports electrical connectors, terminals, and heat-exchanger components. Its stability under repeated thermal cycling prevents deformation and ensures consistent performance. - Aesthetic Appeal
The warm, golden hue of brass adds a premium look to decorative hardware, lighting fixtures, and musical instruments. Its polishability enables mirror-like finishes without additional cladding or plating. - Antimicrobial Properties
Emerging studies highlight brass’s ability to inhibit microbial growth, making it a preferred material for medical equipment, touch surfaces (like door handles), and sanitary fittings.
Custom CNC Machining Processes
Producing custom brass components involves several key CNC processes, each tailored to achieve exact specifications:
- Turning
- CNC Lathes: Brass bar stock is chucked and rotated at high speed (often 3,000–10,000 RPM) while a precision cutting tool shapes shafts, bushings, threaded fittings, and stepped diameters.
- Live Tooling Lathes: Equipped with rotating tooling, these machines perform milling, drilling, and tapping operations in one setup, reducing part handling and improving accuracy.
- Milling
- 3-Axis Milling: Standard for pockets, slots, and flat faces.
- 4- & 5-Axis Milling: Enables complex contours, undercuts, and multi-surface machining in a single setup—ideal for valve bodies, sensor housings, and decorative components.
- Drilling & Tapping
- Automated drilling cycles produce precise hole patterns, while synchronized tapping tools create internal threads to exact depth and pitch, ensuring leak-free fittings and reliable fastener engagement.
- Broaching & Reaming
- For high-precision internal profiles (e.g., keyways) and smooth hole finishes, broaching and reaming operations can be integrated into CNC workflows.
- Deburring & Finishing
- Vibratory Tumbling: Removes burrs and polishes multiple parts simultaneously.
- Hand Polishing: Achieves mirror finishes on decorative pieces.
- Ultrasonic Cleaning: Eliminates micro-debris and ensures parts meet stringent cleanliness standards for medical or electronic applications.
Industries and Applications
Custom brass CNC machined parts find homes in a vast array of sectors:
- Electronics & Telecommunications
Connectors, PCB standoffs, RF adapters, and terminal blocks leverage brass’s conductivity and dimensional stability. - Automotive & Transportation
Fuel-line fittings, sensor housings, transmission bushings, and dashboard components benefit from brass’s wear resistance and corrosion protection. - Plumbing & HVAC
Valves, couplings, nozzles, thermostatic elements, and manifolds exploit brass’s durability in water, refrigerant, and steam systems. - Medical & Pharmaceutical
Surgical instrument components, inhaler valves, and dialysis connectors use brass for its antimicrobial properties and biocompatibility. - Aerospace & Defense
Fluid connectors, instrumentation fittings, and electrical terminals demand the high tolerances and reliability that brass CNC machining provides. - Decorative & Musical Instruments
Lighting fixtures, door hardware, trumpet valves, and mouthpieces showcase brass’s aesthetic appeal and acoustic resonance.
Ensuring Durability and Accuracy
To guarantee that your custom brass CNC machined parts meet stringent performance requirements, consider these best practices:
- Material Selection
- C36000 for general-purpose machining and intricate details.
- C26000 (70/30 Brass) for enhanced strength and corrosion resistance.
- C46400 (Naval Brass) for marine environments, thanks to tin additions that boost durability.
- Tolerance Management
Discuss required tolerances with your machinist. Critical dimensions often need ±0.01 mm accuracy, while less critical features can allow broader tolerances to reduce cost. - Tooling and Fixturing
- High-Quality Cutting Tools: Carbide or coated tools resist wear and maintain sharpness.
- Custom Fixtures: Ensure repeatable part orientation and minimize deflection under cutting forces, preserving geometric integrity.
- Process Optimization
- Leverage CAM Software for tool-path simulation, collision detection, and machining strategy optimization.
- Use In-Process Inspection (e.g., touch probes) to verify dimensions mid-cycle and adjust parameters in real time.
- Quality Assurance
- Implement Statistical Process Control (SPC) to monitor key dimensions.
- Utilize Coordinate Measuring Machines (CMM) for final inspection and certification.
- Provide First Article Inspection Reports (FAIR) for new parts or revised designs.
Choosing the Right CNC Machining Partner
Your supplier’s expertise directly impacts the quality of your brass components. Look for:
- ISO Certification & Industry Standards
ISO 9001 and relevant certifications (e.g., ISO 13485 for medical devices) demonstrate a commitment to quality management. - CAD/CAM Capabilities
In-house engineering support and sophisticated CAM systems ensure seamless translation from design files (STEP, IGES, SolidWorks) to machine code. - Prototype-to-Production Flexibility
A partner that accommodates low-volume prototyping and high-volume production helps you validate designs before scaling. - On-Site Finishing
Integrated deburring, polishing, plating, and cleaning operations reduce lead times and maintain accountability. - Responsive Communication
Clear project management, quick quotations, and regular updates keep your supply chain on track.
Conclusion
When you get durable and accurate custom brass CNC machined parts, you’re investing in components that combine the inherent advantages of brass with state-of-the-art automation. From tight tolerances and corrosion resistance to outstanding electrical performance and aesthetic appeal, brass CNC parts deliver consistent, high-quality results across diverse industries. By partnering with a certified, experienced machine shop that embraces modern tooling, CAM software, and rigorous quality control, you ensure your projects benefit from on-time delivery, cost-effective production, and unmatched reliability—letting you focus on innovation, not manufacturing challenges.
Source: Get Durable and Accurate Custom Brass CNC Machined Parts